Belægningsmetoderne for fotoresist er generelt opdelt i spincoating, dyppecoating og valsecoating, blandt hvilke spincoating er den mest almindeligt anvendte. Ved spincoating dryppes fotoresist på substratet, og substratet kan roteres ved høj hastighed for at opnå en fotoresistfilm. Derefter kan en fast film opnås ved at opvarme den på en varmeplade. Spin-coating er velegnet til coating fra ultratynde film (ca. 20nm) til tykke film på omkring 100um. Dens egenskaber er god ensartethed, ensartet filmtykkelse mellem wafere, få defekter osv., og en film med høj belægningsydeevne kan opnås.
Spin coating proces
Under spincoating bestemmer substratets hovedrotationshastighed filmtykkelsen af fotoresisten. Forholdet mellem rotationshastigheden og filmtykkelsen er som følger:
Spin=kTn
I formlen er Spin rotationshastigheden; T er filmtykkelsen; k og n er konstanter.
Faktorer, der påvirker spincoatingprocessen
Selvom filmtykkelsen bestemmes af hovedrotationshastigheden, er den også relateret til stuetemperatur, fugtighed, fotoresistviskositet og fotoresisttype. Sammenligning af forskellige typer fotoresistbelægningskurver er vist i figur 1.
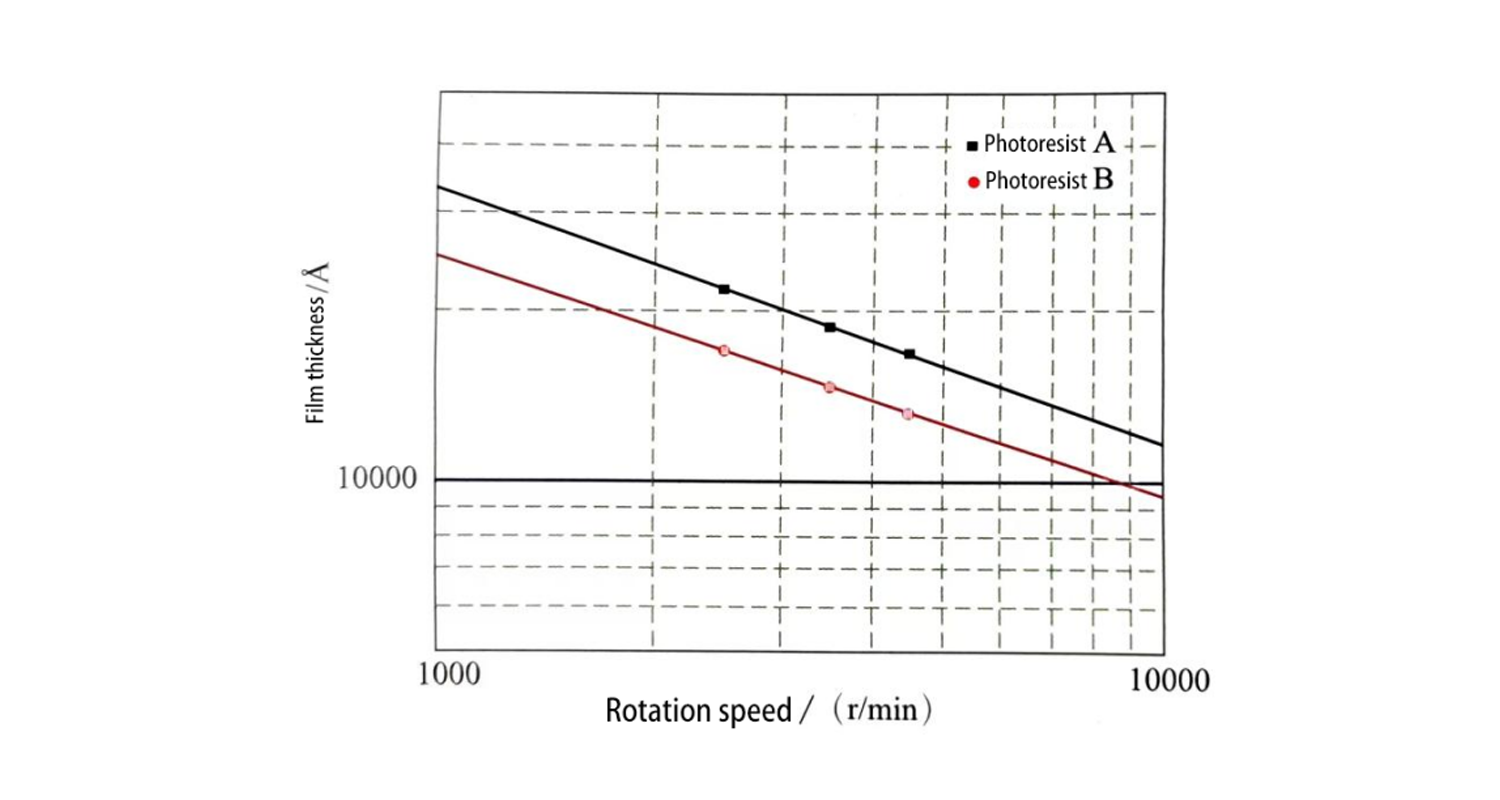
Figur 1: Sammenligning af forskellige typer fotoresistbelægningskurver
Påvirkningen af hovedrotationstiden
Jo kortere hovedrotationstiden er, jo tykkere filmtykkelse. Når hovedrotationstiden øges, jo tyndere bliver filmen. Når den overstiger 20s, forbliver filmtykkelsen næsten uændret. Derfor vælges hovedrotationstiden normalt til at være mere end 20 sekunder. Forholdet mellem hovedrotationstiden og filmtykkelsen er vist i figur 2.
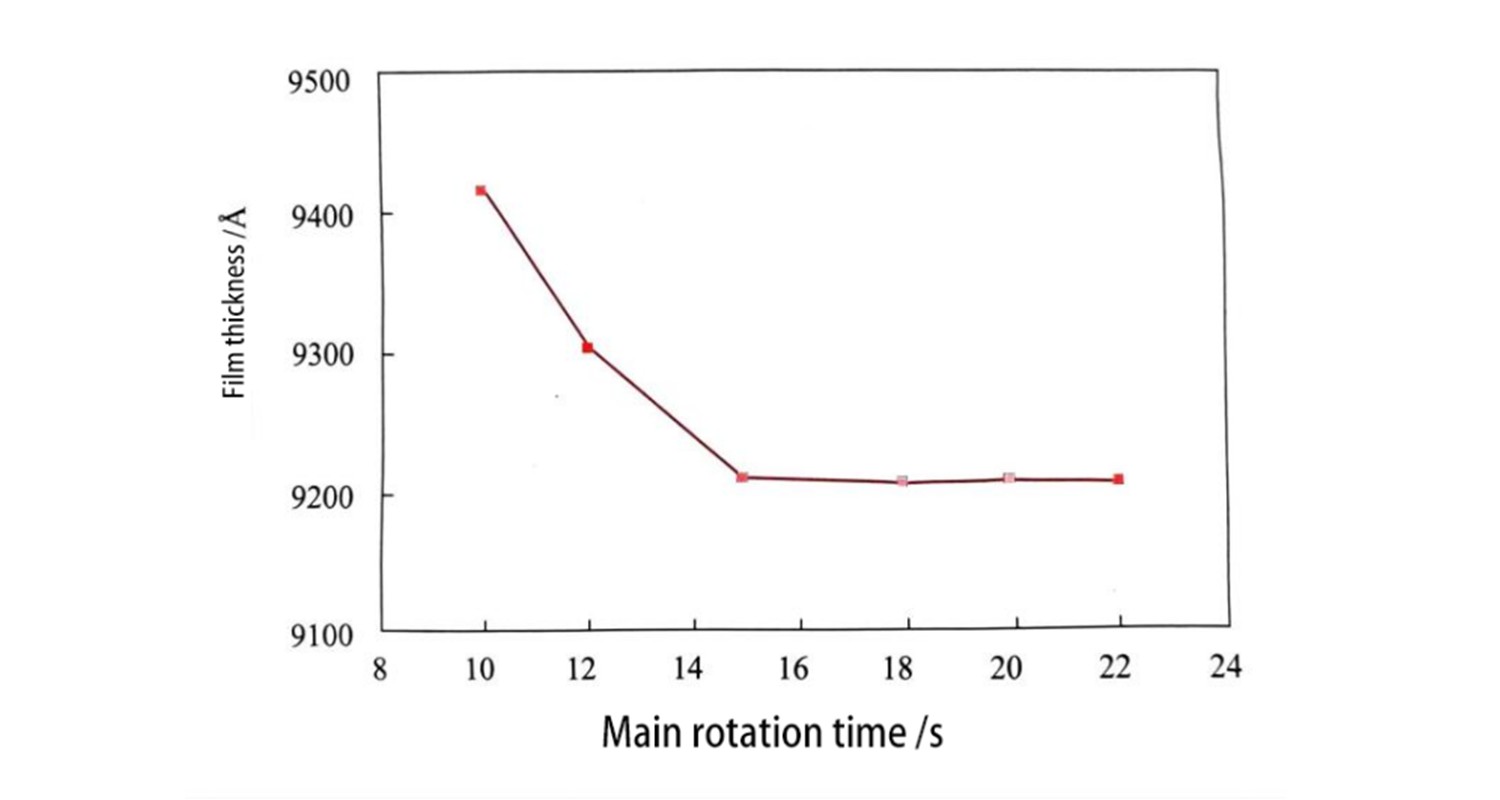
Figur 2: Sammenhæng mellem hovedrotationstid og filmtykkelse
Når fotoresisten dryppes på substratet, selv hvis den efterfølgende hovedrotationshastighed er den samme, vil substratets rotationshastighed under drypningen påvirke den endelige filmtykkelse. Tykkelsen af fotoresistfilmen øges med stigningen af substratets rotationshastighed under drypningen, hvilket skyldes påvirkningen af opløsningsmiddelfordampning, når fotoresisten foldes ud efter drypning. Figur 3 viser forholdet mellem filmtykkelsen og hovedrotationshastigheden ved forskellige substratrotationshastigheder under fotoresistdrypningen. Det kan ses af figuren, at med stigningen af rotationshastigheden af det dryppende substrat, ændres filmtykkelsen hurtigere, og forskellen er mere tydelig i området med lavere hovedrotationshastighed.
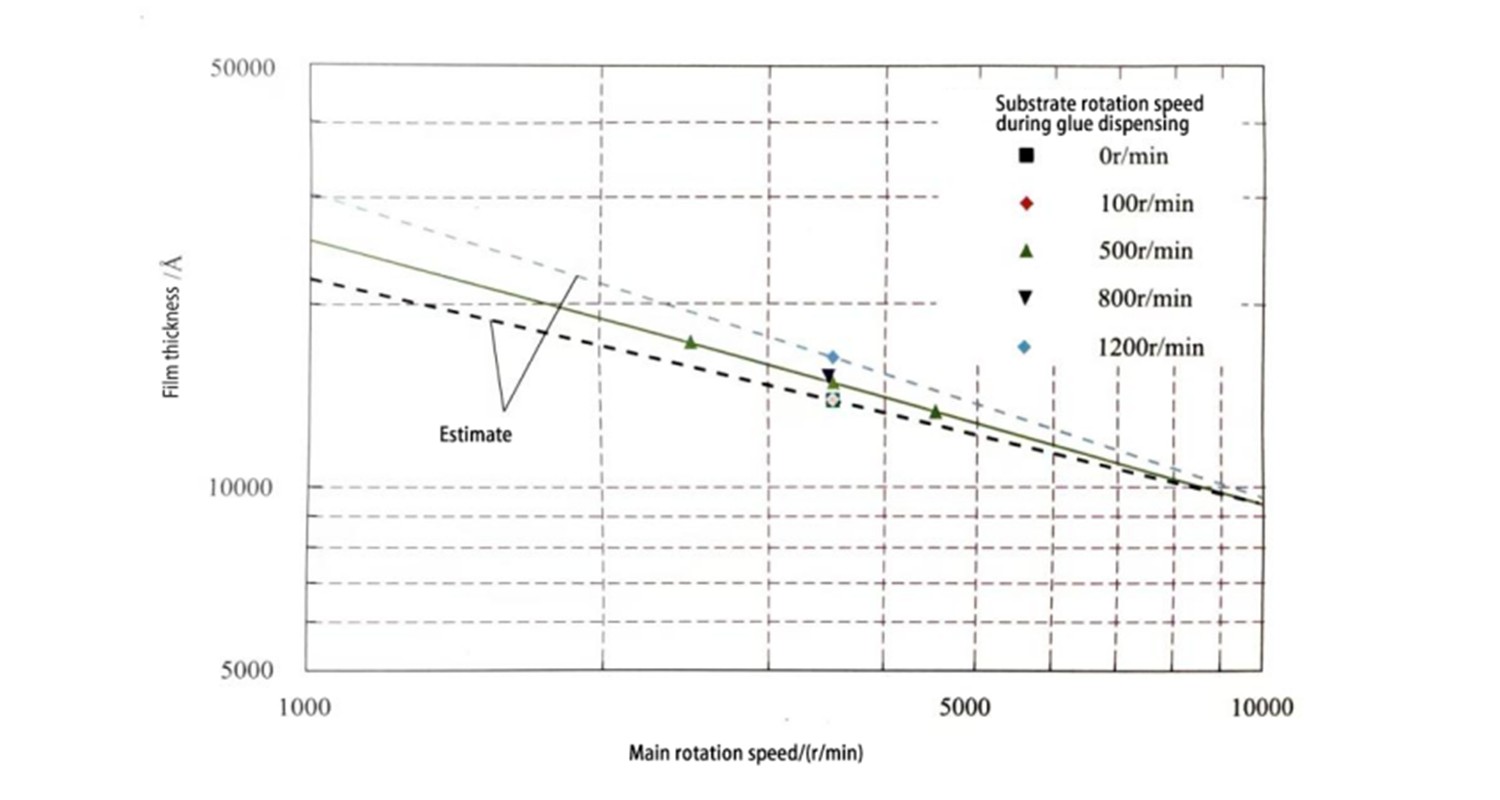
Figur 3: Forholdet mellem filmtykkelse og hovedrotationshastighed ved forskellige substratrotationshastigheder under fotoresistdispensering
Effekt af fugt under belægning
Når fugtigheden falder, øges filmtykkelsen, fordi faldet i fugtigheden fremmer fordampningen af opløsningsmidlet. Filmtykkelsesfordelingen ændres dog ikke væsentligt. Figur 4 viser forholdet mellem fugtighed og filmtykkelsesfordeling under belægning.
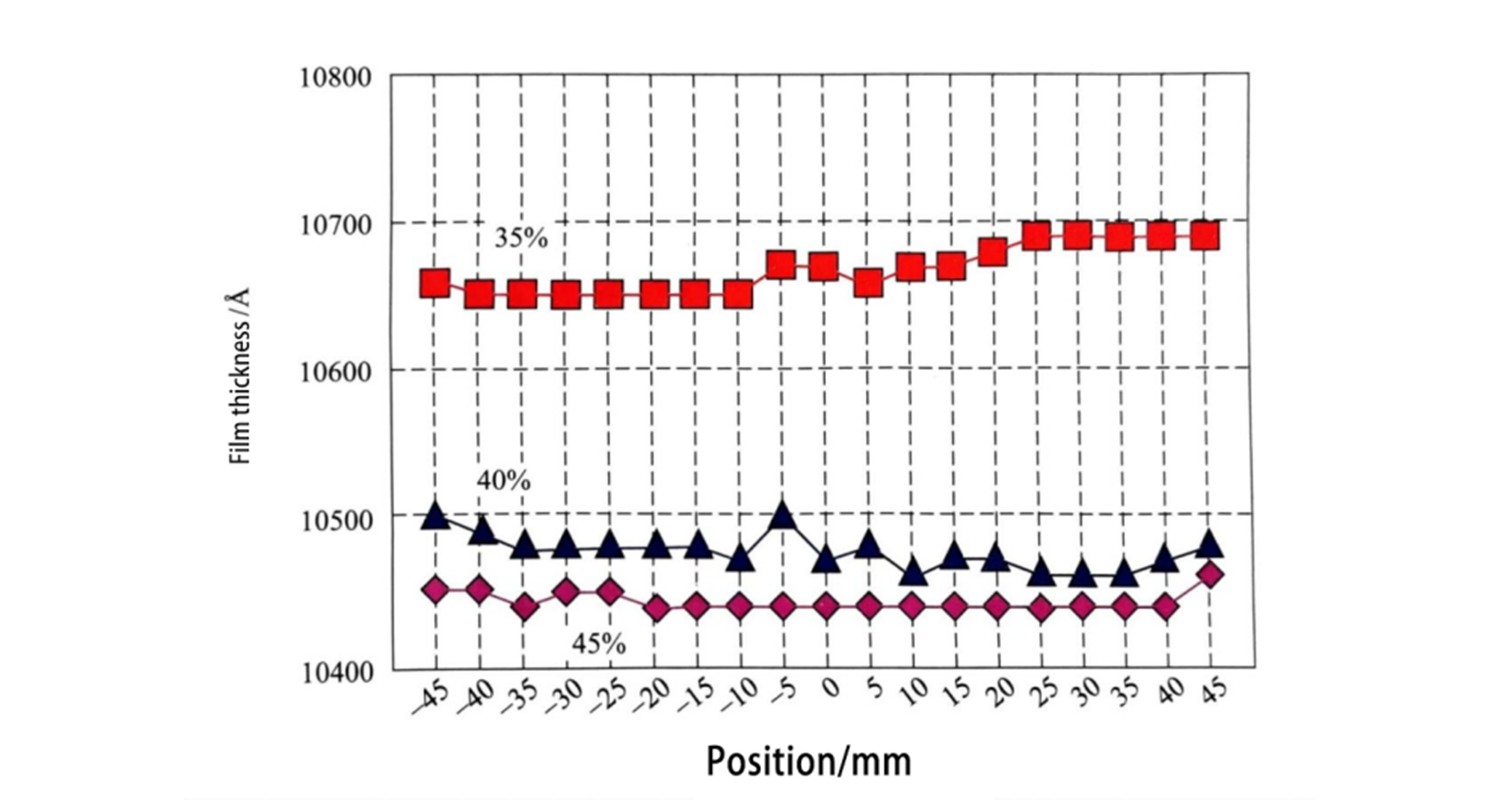
Figur 4: Sammenhæng mellem fugt og filmtykkelsesfordeling under belægning
Effekt af temperatur under belægning
Når indetemperaturen stiger, øges filmtykkelsen. Det kan ses af figur 5, at fordelingen af fotoresistfilmtykkelsen ændres fra konveks til konkav. Kurven i figuren viser også, at den højeste ensartethed opnås, når indetemperaturen er 26°C og fotoresisttemperaturen er 21°C.
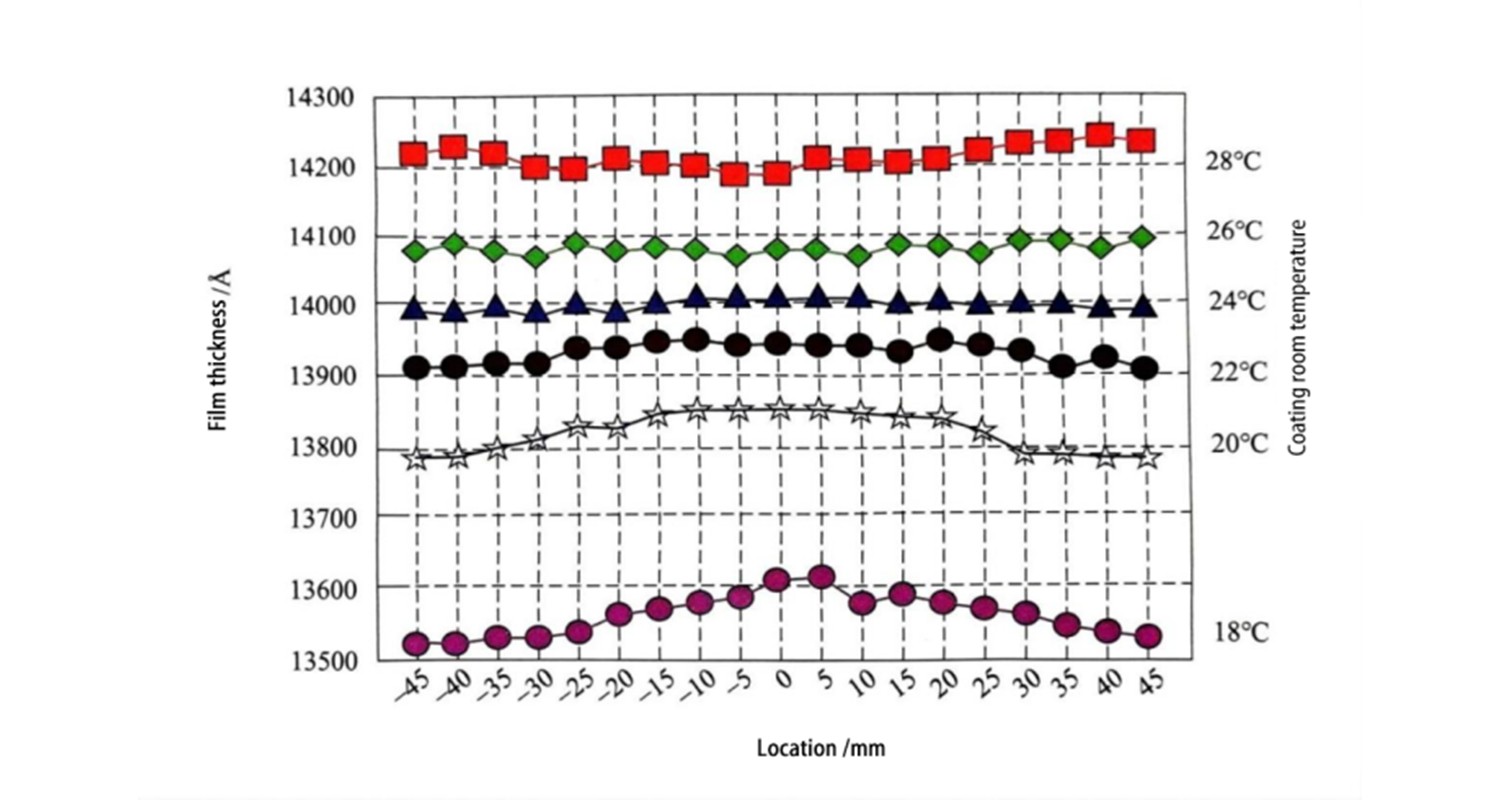
Figur 5: Sammenhæng mellem temperatur og filmtykkelsesfordeling under belægning
Effekt af udstødningshastighed under belægning
Figur 6 viser forholdet mellem udstødningshastighed og filmtykkelsesfordeling. I fravær af udstødning viser det, at midten af waferen har en tendens til at blive tykkere. Forøgelse af udstødningshastigheden vil forbedre ensartetheden, men hvis den øges for meget, vil ensartetheden falde. Det kan ses, at der er en optimal værdi for udstødningshastigheden.
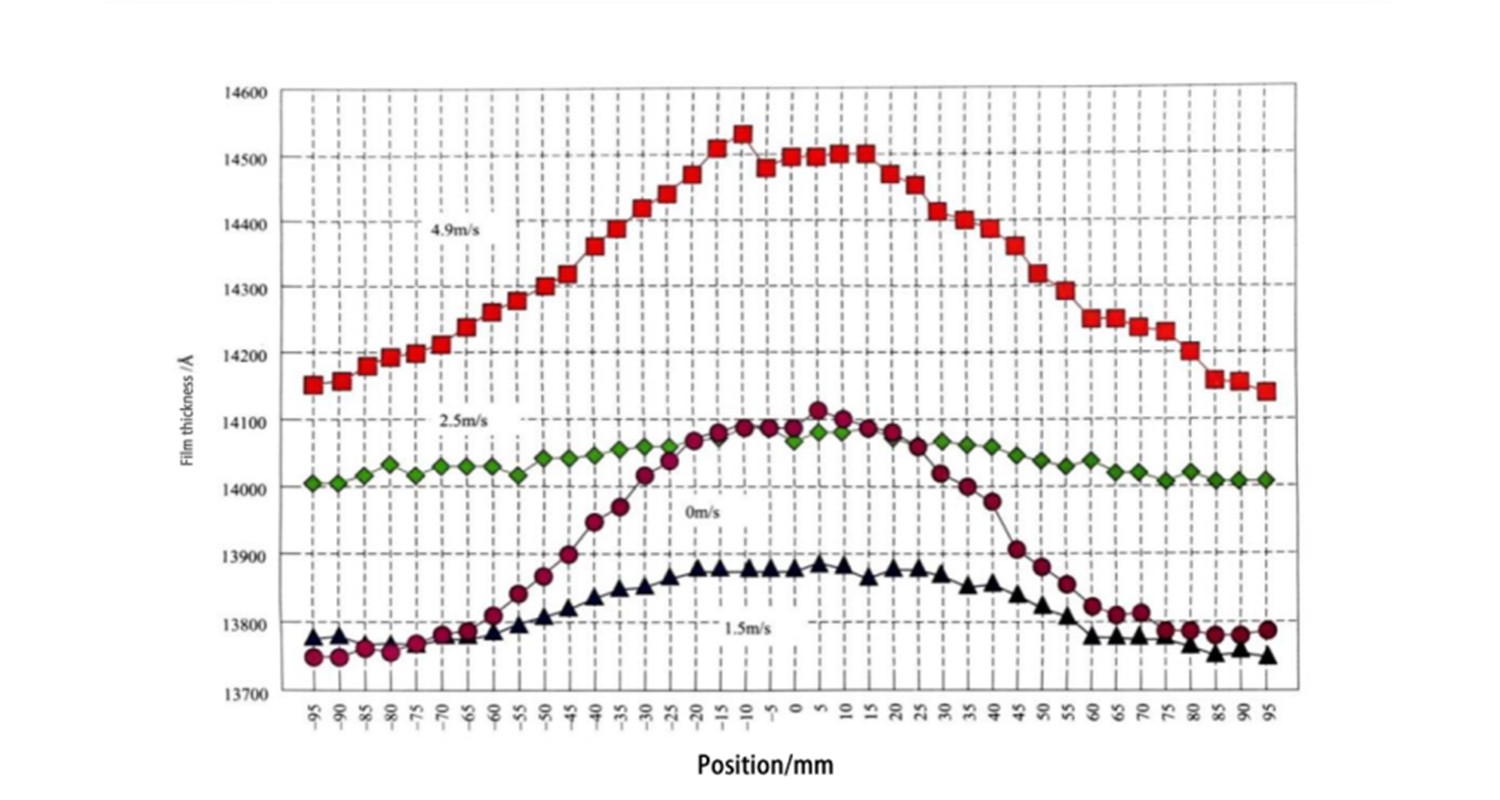
Figur 6: Sammenhæng mellem udstødningshastighed og filmtykkelsesfordeling
HMDS behandling
For at gøre fotoresisten mere belægningsdygtig, skal waferen behandles med hexamethyldisilazan (HMDS). Især når fugt er bundet til overfladen af Si-oxidfilmen, dannes silanol, hvilket reducerer vedhæftningen af fotoresisten. For at fjerne fugt og nedbryde silanol opvarmes waferen normalt til 100-120°C, og tåge HMDS indføres for at forårsage en kemisk reaktion. Reaktionsmekanismen er vist i figur 7. Gennem HMDS-behandling bliver den hydrofile overflade med en lille kontaktvinkel en hydrofob overflade med en stor kontaktvinkel. Opvarmning af waferen kan opnå højere fotoresist-vedhæftning.
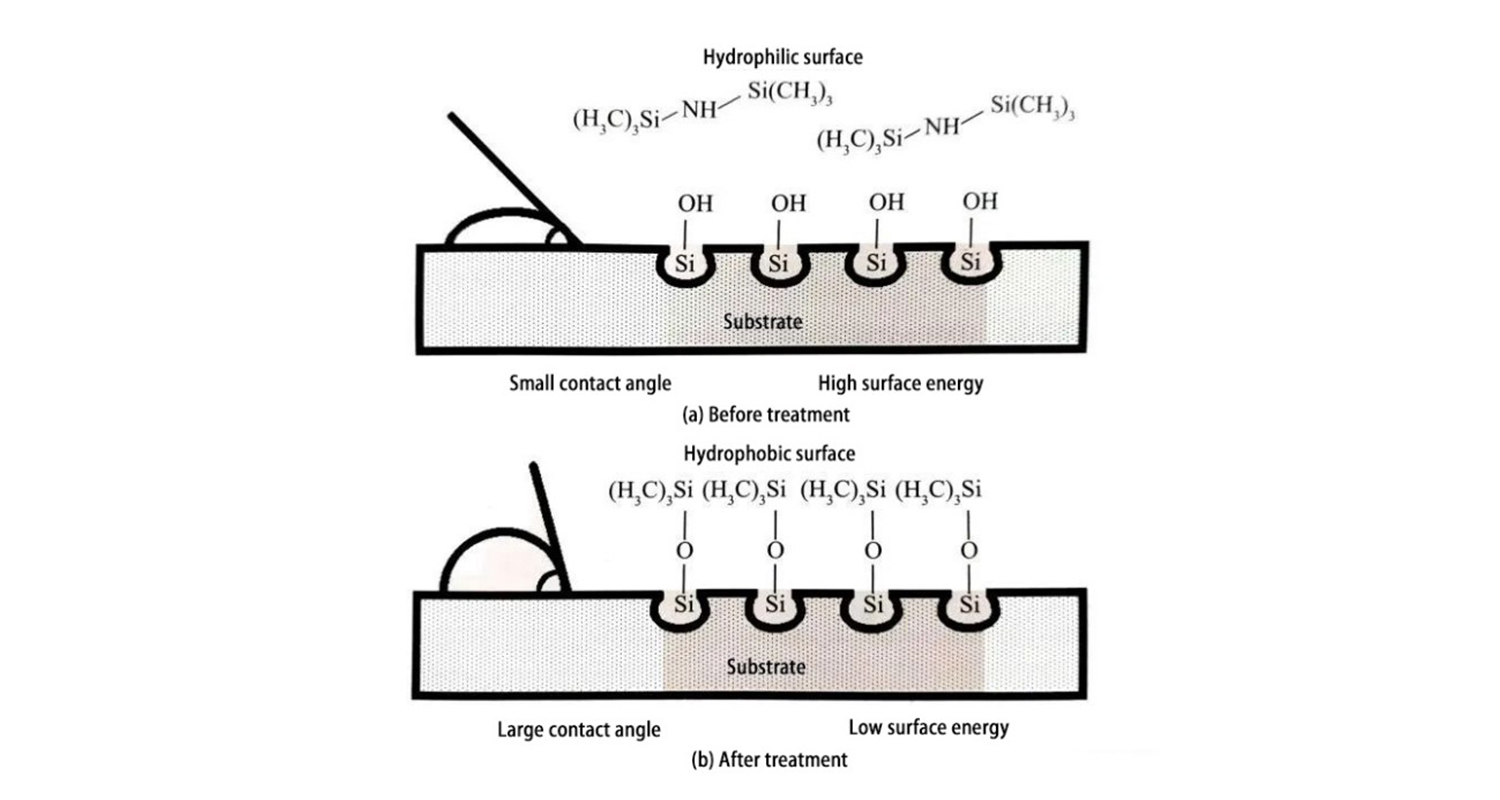
Figur 7: HMDS-reaktionsmekanisme
Effekten af HMDS-behandling kan observeres ved at måle kontaktvinklen. Figur 8 viser forholdet mellem HMDS-behandlingstid og kontaktvinkel (behandlingstemperatur 110°C). Substratet er Si, HMDS-behandlingstiden er mere end 1 min., kontaktvinklen er større end 80°, og behandlingseffekten er stabil. Figur 9 viser forholdet mellem HMDS-behandlingstemperatur og kontaktvinkel (behandlingstid 60s). Når temperaturen overstiger 120 ℃, falder kontaktvinklen, hvilket indikerer, at HMDS nedbrydes på grund af varme. Derfor udføres HMDS-behandling normalt ved 100-110 ℃.
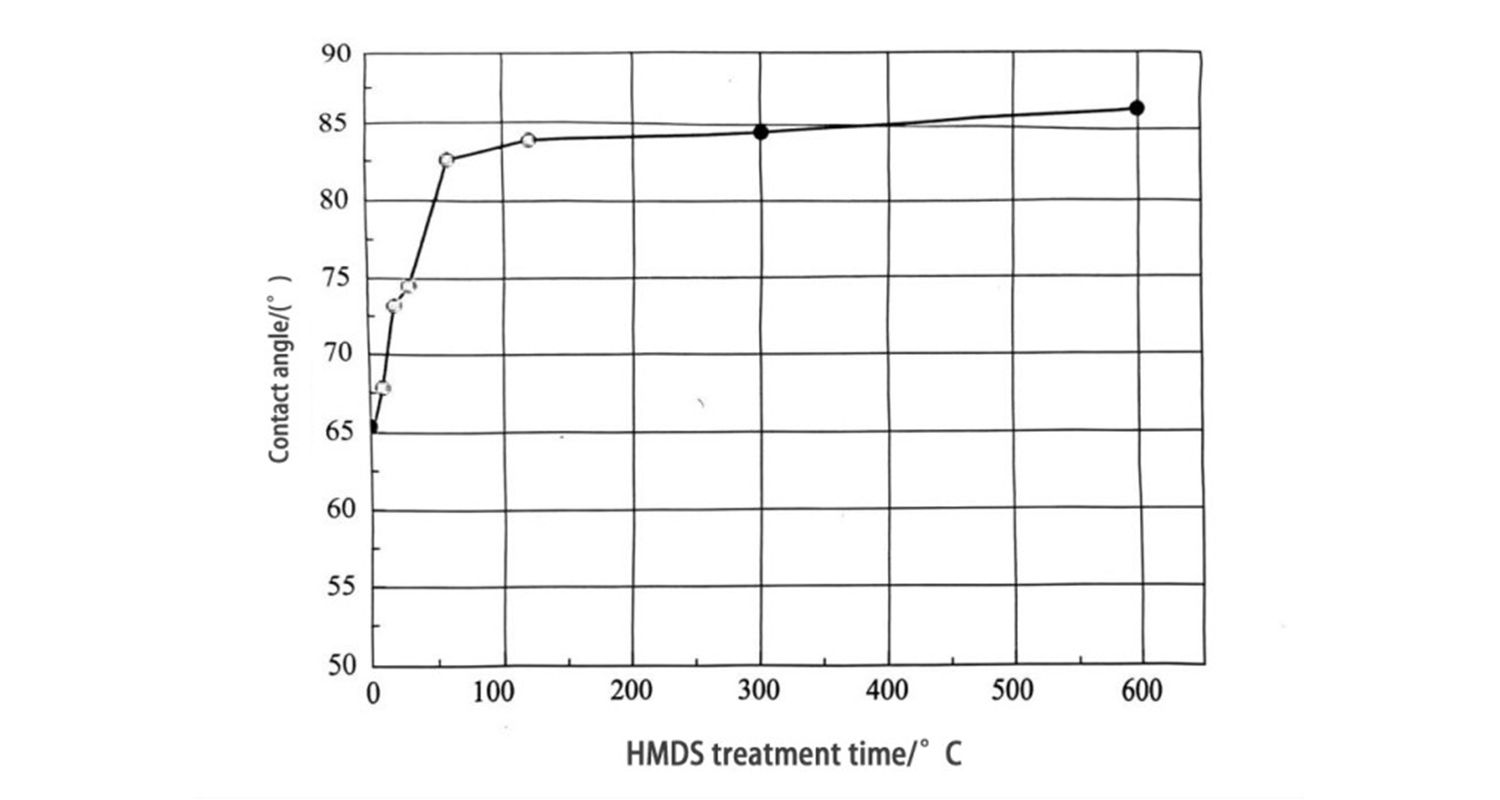
Figur 8: Sammenhæng mellem HMDS-behandlingstid
og kontaktvinkel (behandlingstemperatur 110 ℃)
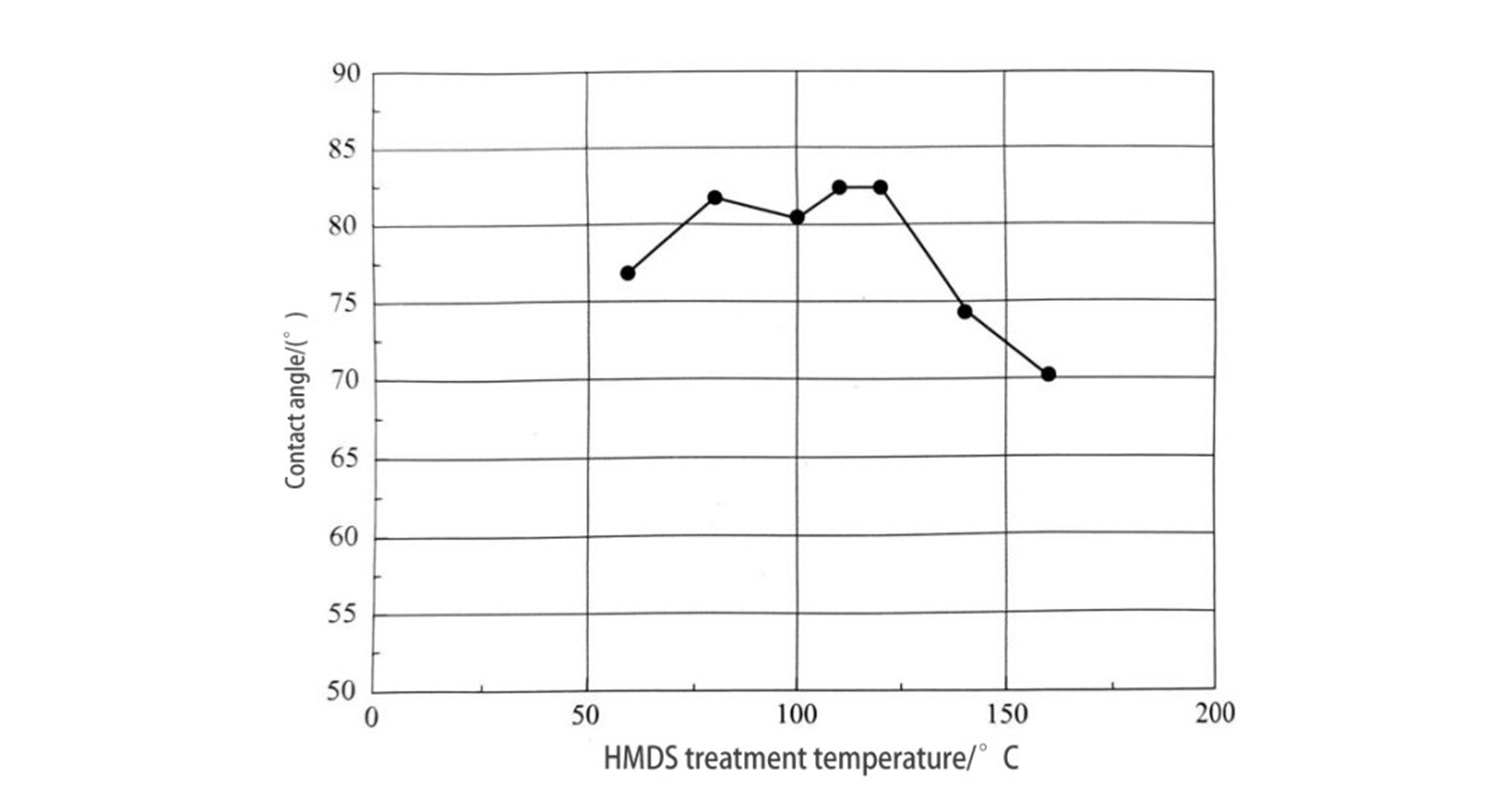
Figur 9: Sammenhæng mellem HMDS behandlingstemperatur og kontaktvinkel (behandlingstid 60s)
HMDS-behandling udføres på et siliciumsubstrat med en oxidfilm for at danne et fotoresistmønster. Oxidfilmen ætses derefter med flussyre tilsat en buffer, og det viser sig, at efter HMDS-behandling kan fotoresistmønsteret forhindres i at falde af. Figur 10 viser effekten af HMDS-behandling (mønsterstørrelsen er 1um).
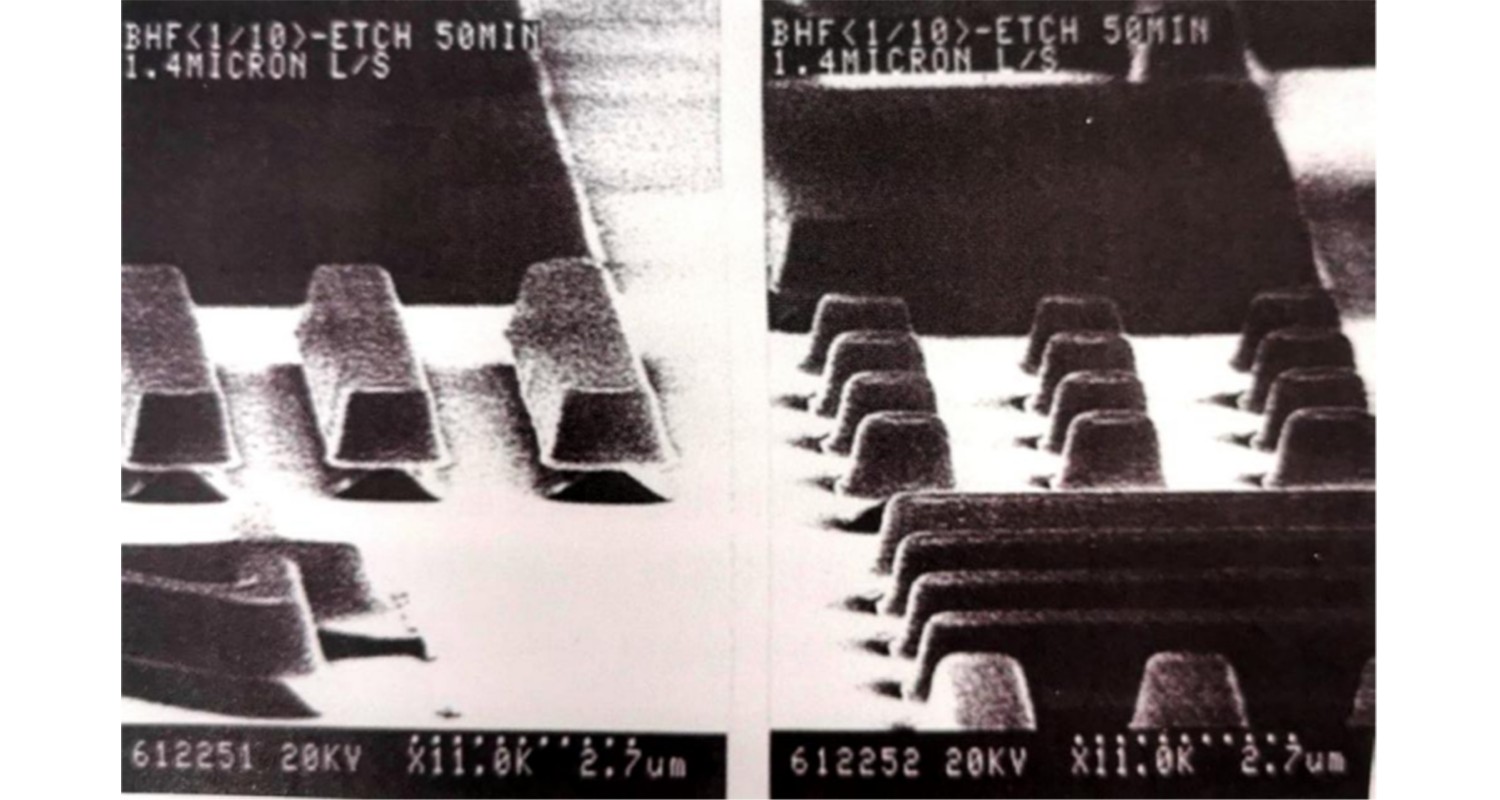
Figur 10: HMDS-behandlingseffekt (mønsterstørrelsen er 1um)
Forbagning
Ved samme rotationshastighed, jo højere forbagningstemperatur, jo mindre filmtykkelse, hvilket indikerer, at jo højere forbagningstemperatur, jo mere opløsningsmiddel fordamper, hvilket resulterer i en tyndere filmtykkelse. Figur 11 viser forholdet mellem forbagningstemperaturen og Dilds A-parameter. A-parameteren angiver koncentrationen af det lysfølsomme middel. Som det kan ses af figuren, når forbagningstemperaturen stiger til over 140°C, falder A-parameteren, hvilket indikerer, at det lysfølsomme middel nedbrydes ved en temperatur højere end dette. Figur 12 viser den spektrale transmittans ved forskellige forbagningstemperaturer. Ved 160°C og 180°C kan en stigning i transmittans observeres i bølgelængdeområdet 300-500nm. Dette bekræfter, at det lysfølsomme middel er bagt og nedbrudt ved høje temperaturer. Forbagningstemperaturen har en optimal værdi, som bestemmes af lysegenskaber og følsomhed.
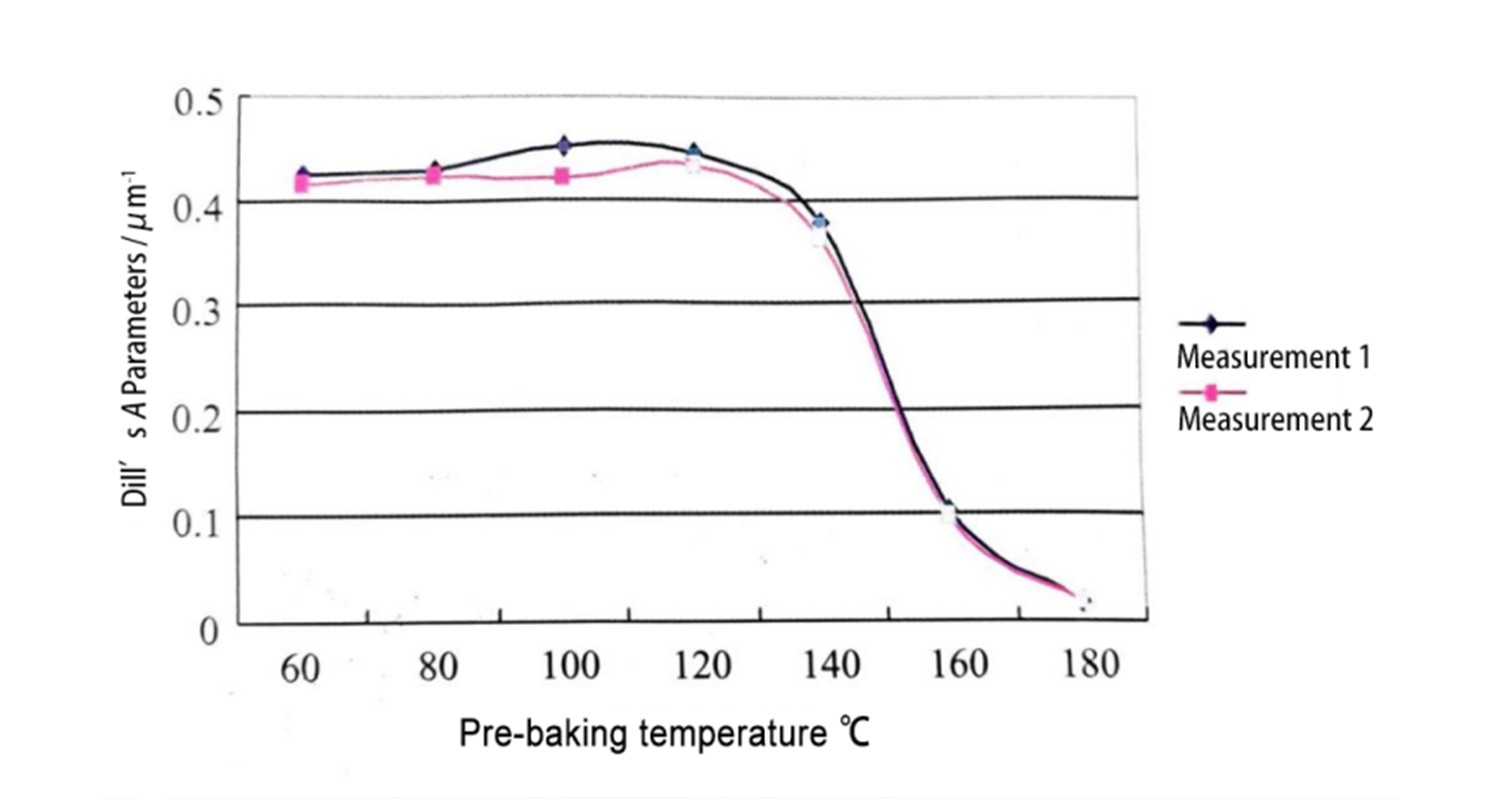
Figur 11: Sammenhæng mellem forbagningstemperatur og Dilds A-parameter
(målt værdi af OFPR-800/2)
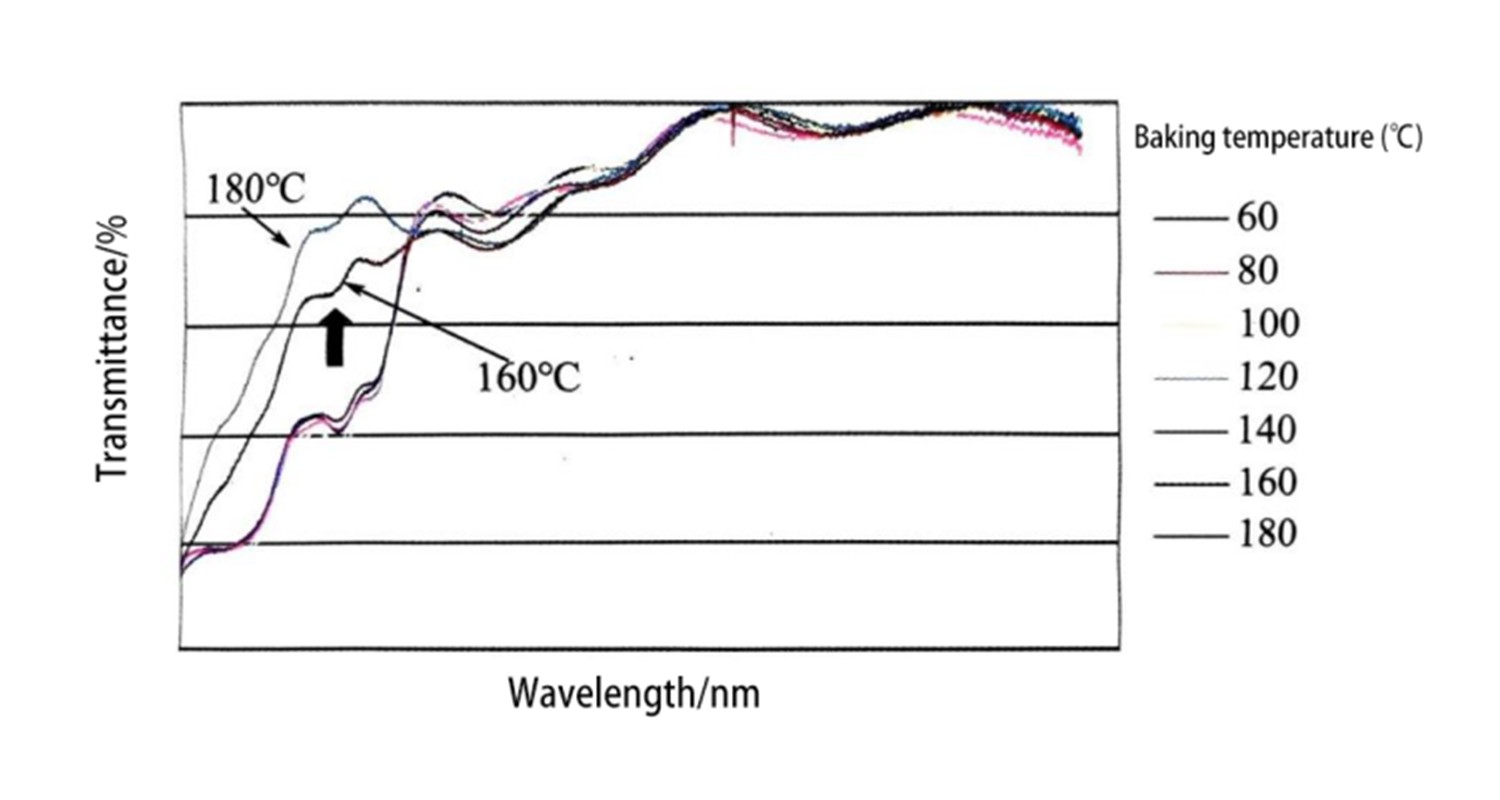
Figur 12: Spektral transmittans ved forskellige forbagningstemperaturer
(OFPR-800, 1um filmtykkelse)
Kort sagt har spincoating-metoden unikke fordele, såsom præcis kontrol af filmtykkelse, høj omkostningsydelse, milde procesforhold og enkel betjening, så den har betydelige effekter på at reducere forurening, spare energi og forbedre omkostningsydelsen. I de senere år har spincoating fået stigende opmærksomhed, og dens anvendelse har gradvist spredt sig til forskellige områder.
Indlægstid: 27. november 2024